AJRAKH
The art of Block Printing and other forms of Fabric dyeing & printing has evolved in India over centuries has depicted civilisations evolved in different times. It can be put other way as a connecting link between civilization.
Ajrak or Ajrakh, is a unique form of a wood block printing originated in Sindh, now in Pakistan and is also being practiced in Ajrakhpur in Kutch, district of India. Sindh had abundance of Cotton crop, Indigo plantation and river water.
With the naturally available resources a 3000 year old craft has been a distinct identity of Sindhi Community. The art with geometrical prints mainly with the base dye Indigo yields respect for consumers as it is symbol of richness and also gesture of respect to the guest. It can also be called Rhythm of Blue from nature.
It is widely being used in turbans or dupattas the art also is popular amongst the other adorable fashion fabric.
Considerably a pretty long process is performed on the fabric to make the fashion wear suit the taste of modern consumers. The process involves steps like
Saaj:
It is a washing process of cloth to remove starch and finish of mill/weaving unit. The cloth is soaked in solution of Camel Dung, Soda Ash & castor oil. It is then wrung out and kept overnight. The cloth is semidried in sun light and again the process is repeated. Usually the process is repeated for 7-8 times to get the desired cleaning of impurities for good printing result.
Kasano:
Kasano is a mordanting process. The cloth is washed in Myrobalan solution and dried in the sunlight. It is the 1st mordanting process in Ajrakh printing art.
Khariyano:
A resist solution of lime and Gum Arabic is printed with the help of wooden blocks to create outline of white. This lines / process is called Rekh. The blocks have symmetrical registration mark to enable two sided printing.
Kat:
Kat is a paste of scrap iron, jaggery & water. The mixture is left for 20days. Thus prepared ferrous water then mixed with tamarind seed powder and boiled into a paste of it. This paste is called Kat. The paste is used for printing Black colour.
Gach:
Alum, Gum Arabic & clay are mixed into the paste for next resist printing. Also the resit of lime and Gum Arabic is used this time. The combined process is known as Gach. The saw dust is sprinkled over the printed area and let the fabric dry for about 3-4 days.
Indigo Dyeing:
After the Gach the cloth is dyed in Indigo. For uniformity the Indigo dyeing is done twice.
Vicharnu:
After indie dyeing the cloth is washed to remove any resist and unfixed dye.
Rang:
After all above process the fabric is dipped & boiled in to Alizarin to get the alum-residue area a get red colour. Grey area from the kat/gach stage gives deep colour. For different colour the fabric id boiled in different dye.
Thus 8 lengthy and time consuming process delivers the artful fabric for consumers.
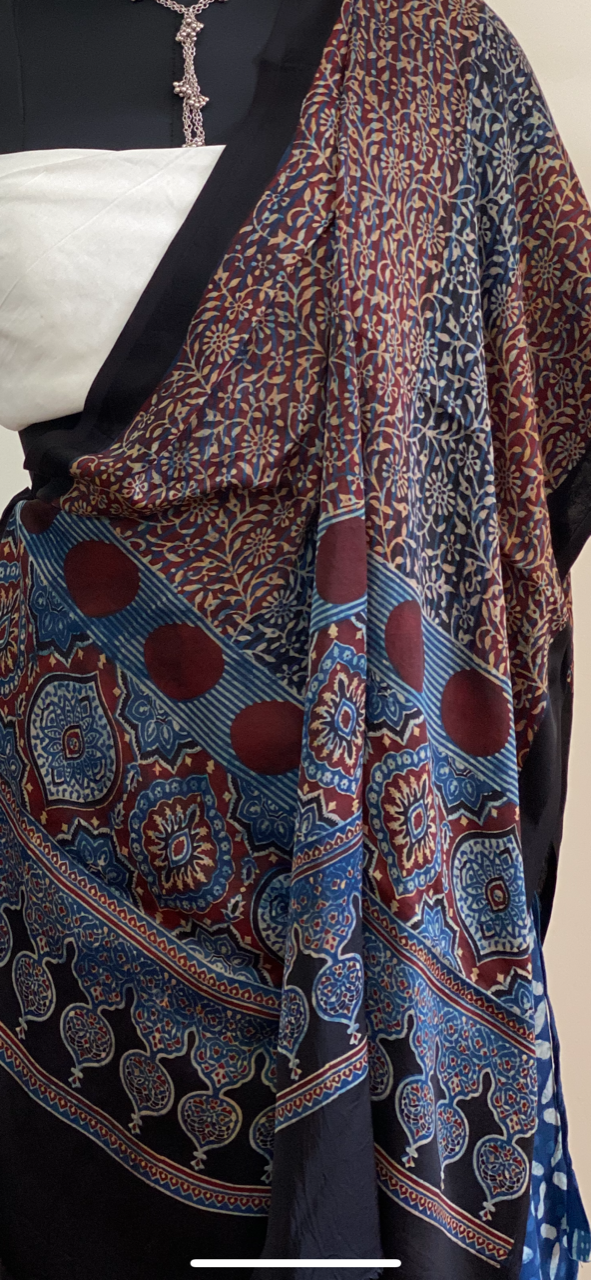
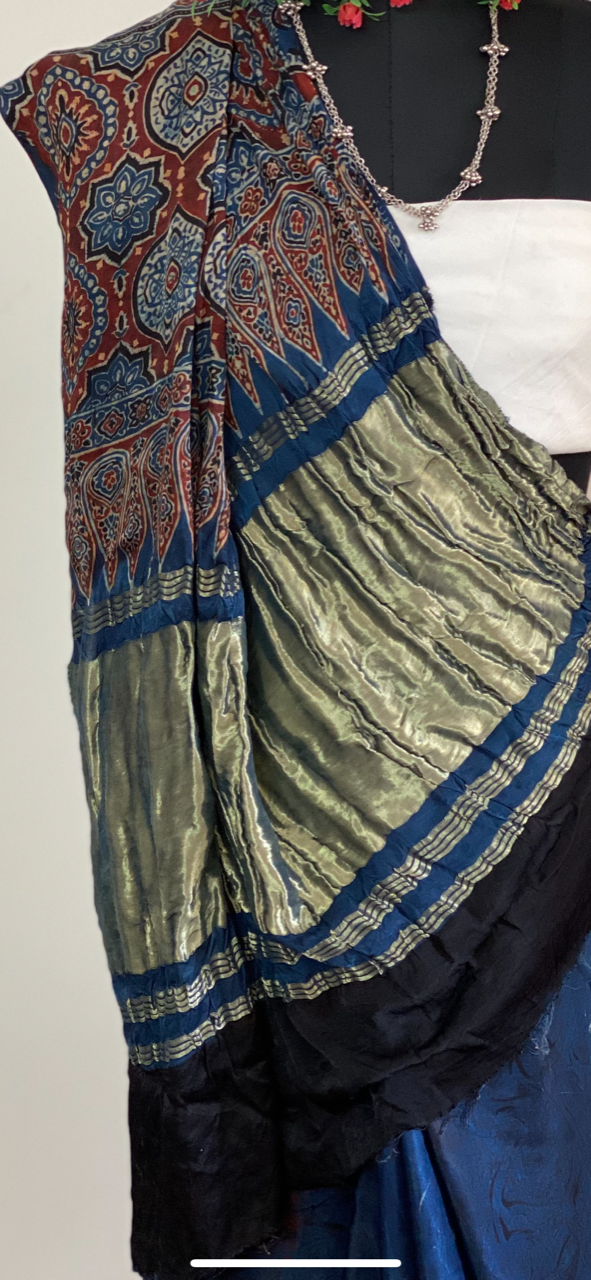